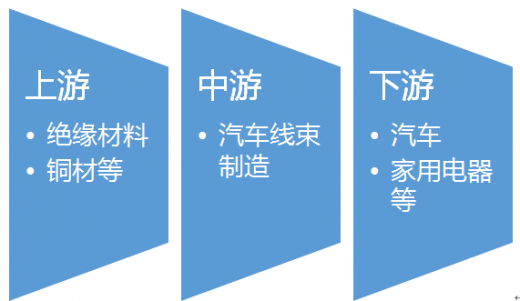
参考观研天下发布《2018-2023年中国汽车产业市场竞争现状调查与投资价值前景评估报告》
二、汽车线束行业上游市场发展情况1、绝缘材料
我国绝缘材料行业起步相对较晚,经过50多年的发展,已初步形成一个产品比较齐全,配套比较完备,具有相当生产规模和科研实力的工业体系。特别是进入21世纪以来,随着国民经济的快速增长,发电、输变电和电机行业迅猛发展,推动我国的绝缘材料行业的强劲发展。目前,全国绝缘材料生产企业和科研单位超过800家。同时,随着国内绝缘材料生产企业技术水平的不断提高,部分产品已经达到较高水平,在国际市场上具有较强的竞争能力。
近年来,绝缘材料的创新应用逐渐成为我国推行可持续能源方案的关键动力之一,国家对绝缘材料的发展也日益重视。随着电力、电器、电子、通讯和家电等行业的快速发展,我国绝缘材料产品的产销量持续增长。
2014年中国绝缘制品产量为192.21万吨,同比增长10.8%,2015年中国绝缘制品产量为213.93万吨,同比增长11.3%,2016年中国绝缘制品产量为234.89万吨,同比下降234.89%。
时间 |
年度产量:万吨 |
同比增长(%) |
2010年 |
121.32 |
10.9 |
2011年 |
134.18 |
10.6 |
2012年 |
158.6 |
18.2 |
2013年 |
173.51 |
9.4 |
2014年 |
192.21 |
10.8 |
2015年 |
213.93 |
11.3 |
2016年 |
234.89 |
9.8 |
变压器作为电网中电力传送过程的主要电力设备,是电气成套设备领域最常见的器件之一。在变压器行业,我国市场增长迅速,目前已成为国际第二大市场,随着我国电力需求增长迅速,电网的高速建设拉动了输变电设备的市场需求。变压器作为电力输送的关键电气设备,市场需求也保持了稳步的增长。
我国变压器行业企业数量非常庞大,目前,我国有资质生产各种变压器的企业大约有2000多家,而工业总产值超过1亿元人民币的只有130余家,员工人数超过2000人的也仅仅只有20家左右。按照工业产值划分,中小型变压器生产制造企业占企业总数的80%以上。多数小企业技术实力不强,只能生产110以下的低端产品,从而导致中低端变压器市场生产能力严重过剩。据统计,目前国内变压器的产能利用率仅为50%。
由于中低端产品本身产品附加值低,再加上供求失衡,直接导致价格不断下滑,很多企业已处于亏损的边缘,经营状况堪忧。变压器行业报告分析认为,目前变压器中低端市场上企业鱼目混杂,价格战下一部分企业以放弃质量为代价,这部分企业必将会被市场所淘汰,行业将面临一轮大洗牌。总体而言,高端市场景气度较高,仍有很大的市场空间。
目前,我国有能力生产500kV级变压器的企业不超过10家,自行独立生产技术水平较先进国家相比还有一定差距,总体技术水平还有待提高;而国内能生产220kV级变压器的企业不超过30家;能生产110kV级变压器的企业则只有100多家;年产超过100百台以上的变压器企业更是凤毛麟角。
从市场格局来看,我国变压器行业呈现金字塔型结构,电压等级越高,技术壁垒就越强,生产厂家越少,垄断程度越高。在新的机遇下,电力变压器市场不断扩大的同时,也要求着变压器产业进行新的升级,特别是在智能化发展的情况下,节能型、智能型变压器的研发、制造、销售、使用、维护将成为主流。
2、铜材
经过多年发展,目前我国已成为世界上重要的铜材生产、消费和贸易大国。2015年度,我国铜材产量达到1,913.70万吨,同比增长7.29%。近十年,我国铜加工行业整体上保持了快速、持续的发展态势。
2006-2015年我国铜材年产量及消费量(单位:万吨)
年份 |
出口量 |
进口量 |
净进口量 |
产量 |
表观消费量 |
2006年 |
55.91 |
109.26 |
53.34 |
564.25 |
617.59 |
2007年 |
49.97 |
105.38 |
55.41 |
662.60 |
718.01 |
2008年 |
51.75 |
93.50 |
41.74 |
784.91 |
826.65 |
2009年 |
45.51 |
82.39 |
36.87 |
980.01 |
1,016.88 |
2010年 |
50.86 |
91.05 |
40.20 |
1,067.10 |
1,107.30 |
2011年 |
50.03 |
78.16 |
28.13 |
1,110.60 |
1,138.73 |
2012年 |
49.30 |
66.86 |
17.55 |
1,168.00 |
1,185.55 |
2013年 |
48.90 |
65.00 |
16.10 |
1,498.70 |
1,514.81 |
2014年 |
50.78 |
60.40 |
9.61 |
1,783.70 |
1,793.31 |
2015年 |
46.61 |
56.33 |
9.72 |
1,913.70 |
1,923.42 |
我国铜材产品产量与表观消费量
省份 |
2011年度 |
2012年度 |
2013年度 |
2014年度 |
2015年度 |
年均增长率 |
浙江 |
189.07 |
214.75 |
249.71 |
296.38 |
332.20 |
15.13% |
江西 |
156.47 |
208.89 |
264.10 |
312.87 |
308.20 |
18.47% |
江苏 |
172.47 |
174.53 |
221.40 |
278.51 |
306.50 |
15.46% |
安徽 |
132.81 |
142.81 |
172.95 |
244.12 |
290.90 |
21.65% |
广东 |
137.98 |
102.53 |
155.00 |
186.06 |
182.00 |
7.17% |
五省合计 |
788.80 |
843.51 |
1,063.16 |
1,317.94 |
1,419.80 |
15.83% |
汽车线束是指由铜材冲制而成的接触件端子(连接器)与电线电缆压接后,外面再塑压绝缘体或外加金属壳体等,以线束捆扎形成连接电路的组件,是汽车内部通讯的基本载体。
按照汽车区域和功能,线束可以分为:
1)发动机线束,连接发动机上的各种传感器和执行器,围绕在发动机的周围。
2)仪表板线束,与车身或者底盘线束连接,沿着管梁行走连接仪表板上的各种电器件如组合仪表、空调开关、收放机、点烟器等。
3)车身线束,一般是从驾驶室的左侧贴着地板行走,连接油箱传感器和后尾灯。
4)门线束,连接门内板上的所有电器件,如中控锁,玻璃升降器,扬声器等。
5)前围线束,从驾驶室过来,沿着翼子板和前保险杠骨架连接前围的电器件如侧转向灯和前组合灯,喇叭、电子风扇等。
汽车线束上能应用到工程塑料的有连接器、紧固件、保险丝盒等等部件,主要使用的材料为PA耐热级、PA增韧级、PA+玻纤、矿粉、玻珠增强级,以及PBT、PPO等。
汽车线束行业发展高度依赖汽车行业,目前大部分品牌车厂拥有自己比较成熟完整的汽车供应链,线束行业厂家与汽车企业的结合相对更加紧密。
全球线束市场中,日本的矢崎和住友电气、藤仓和古河占据了超过60%的市场份额,韩国京信、裕罗、悠进也拥有将近15%的份额,其余市场份额被欧美的莱尼、德尔福、李尔、比克希、阿本斯贝格、科洛普所瓜分。
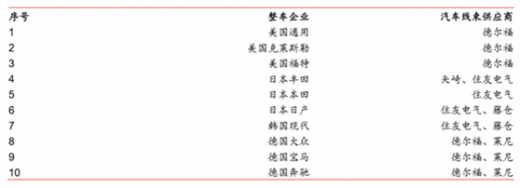
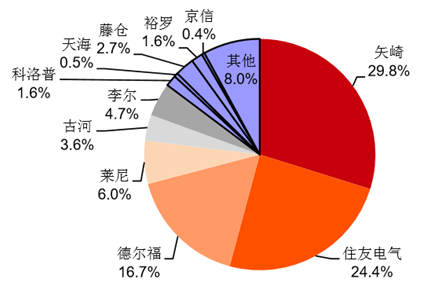
目前国内汽车线束厂家虽然众多,但大多数规模小,研发能力较弱,生产装备落后,质量档次不高,配套车型单一,主要还在为自主品牌在配套。国产线束多为低档车配备,高档、优质线束市场需求广阔。

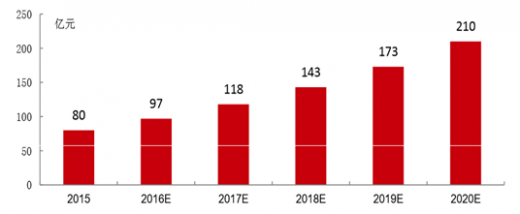
当前,汽车产业正围绕安全、环保、节能的主旋律转型,零部件行业也随之向“低碳化、信息化、智能化”发展,其产品结构、生产方式、服务模式、产业链等都发生了深刻改变。
互联网、信息技术等与零部件产业的深度融合带来了零部件产品的转型升级,零部件行业正在由制造业向服务型制造业转型。在跨界与融合的大背景下,把握住零部件行业的发展脉络,紧跟行业发展趋势至关重要。
伴随汽车工业的蓬勃发展,中国汽车零部件产业规模与生产研发能力在持续提升。一方面,国际零部件巨头的“本土化”战略推进,有效促进了我国汽车零部件产品功能和生产制造水平的提高;另一方面,我国零部件企业加快技术升级,积极参与全球竞争,品牌影响力不断扩大。
数据显示,2015年,中国汽车零部件企业累计实现主营业务收入32117亿元,实现利润总额2464.7亿元,呈现持续稳步增长的态势。
此外,自主创新体系初步形成也是中国零部件行业在发展中的一大亮点。86家汽车零部件上市公司2015年研发支出数据显示,86家公司累计研发投入为132.14亿元,与2014年的125.98亿元同比增长4.89%。动力总成方面,中国自主品牌逐步掌握了缸内直喷、涡轮增压、高压共轨等技术;变速器方面,自主品牌也逐步实现了AT、DCT、CVT等变速器的自主研发和生产,部分产品已经成功投放市场。
虽然汽车零部件产业取得了巨大进步,但整个行业仍存在着数量多、规模小、产业化水平低等问题。比如电控等关键零部件还不能自主研发,部分上游基础产业关键原材料、原器件、装备等还依赖进口。因此自主企业必须重新梳理,动态调整企业战略、产品和技术方向,重新审视发展之路,对现状和趋势进行有效评估。
诚然,尽管中国汽车零部件在产业规模、产业链协同等方面取得了显著成绩,但行业整体发展依然落后于整车,核心技术缺失等问题依然存在,自主品牌零部件企业面临严峻考验。
以自动变速器行业为例,我国大部分自动变速器市场被合资及外资企业占据,自主品牌所占市场份额较小。虽然DCT、AT、CVT等自动变速器都有相关企业进行研发和生产,但部分核心零部件仍需依赖进口,已上市产品可靠性仍待提高。
同时,自主零部件企业采用兼并重组、合资合作、海外并购等方式加速全球化发展,在“走出去”的过程中,零部件企业同样面临激烈竞争与挑战。自主零部件走出去,遇到的问题比较多,应该主要从几个方面来解决。首先是提高产品质量与可靠性,第二是实现现有技术的升级和突破,第三是要结合实际,并把相关服务加以跟进。
新能源汽车与智能网联汽车作为新兴产业,正逐步成为汽车产业中重要的组成部分,相关零部件产业化进程逐步加快,在产品技术、可靠性等方面有显著提高。如新能源汽车零部件,基本形成了以动力电池、电机、电控系统为主的产业链条。数据显示,2015年,我国动力锂电池产量达到15.45GWh,同比增长277.67%。
与此同时,智能网联汽车零部件领域也在迅速发展。自主零部件企业和IT企业纷纷加速布局,力图抢占技术与市场高点。目前在智能网联汽车领域,尤其是信息技术与IT技术领域,国内外差距并不大。自主零部件企业有条件迅速实现转型升级,开发出相应产品。
2017年中国汽车及零部件行业发展趋势
(1)产业转移不断加速
当前,中国、印度等新兴汽车市场已成为世界上市场容量最大、最具增长性的汽车消费市场,同时这些国家劳动力资源丰富、劳动力成本较低、劳动力素质不断提高。随着国际汽车及零部件行业竞争日趋激烈,为了开拓新兴市场,有效降低生产成本,汽车及零部件企业开始加速向中国、印度、东南亚等国家和地区进行产业转移。
(2)采购全球化
在全球经济一体化的背景下,面对竞争日益激烈的市场环境,世界各大汽车公司和零部件供应商在专注于自身核心业务和优势业务的同时,进一步减少汽车零部件的自制率,转而采用全球采购的策略,在世界范围内采购有比较优势的汽车零部件产品。采购全球化已成为当今潮流。
(3)零部件系统的集成化、模块化
汽车零部件系统的集成化、模块化就是通过全新的设计和工艺,将以往由多个零部件分别实现的功能,集成在一个模块组件中,以实现由单个模块组件代替多个零部件的技术手段。汽车零部件系统集成化、模块化具有很多优势,首先,与单个零部件相比,集成化、模块化组件的重量更轻,有利于整机的轻量化,从而达到节能减排的目的;其次,集成化、模块化组件所占的空间更小,能够优化整机的空间布局,从而改善整机性能;再次,与单个零部件相比,集成化、模块化组件减少了安装工序,提高了装配的效率。汽车零部件系统的集成化、模块化已成为汽车零部件行业,尤其是乘用车汽车零部件行业一个重要的趋势。
(4)节能环保新技术的应用
随着全社会对环境问题的日益重视,节能环保技术将成为汽车及零部件行业未来的技术趋势。以燃料电池汽车、混合动力汽车为代表的新能源汽车正在加速发展,汽车零部件的轻量化设计,电子化和智能化设计以及汽车零部件再制造技术等正逐步得到应用。根据相关统计,2015年累计生产新能源汽车37.90万辆,同比增长4倍。节能环保新技术将成为未来汽车零部件产业竞争的制高点。
四、汽车零部件行业下游市场发展现状
据中国汽车工业协会统计,2016年我国汽车产销较快增长,产销总量再创历史新高,全年汽车产销分别完成2811.9万辆和2802.8万辆,比上年同期分别增长14.5%和13.7%,高于上年同期11.2和9.0个百分点。
12月,汽车产销分别完成306.3万辆和305.7万辆,单月销量首次突破300万辆,产销比上月分别增长1.7%和4.0%,比上年同期分别增长15.0%和9.5%。
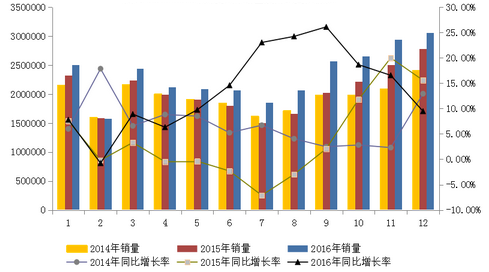
12月乘用车产销分别完成264.4万辆和267.2万辆,产销量比上月分别增长0.2%和3.2%;与上年同期相比,产销量分别增长13.6%和9.1%,产销同比均呈较快增长。其中,轿车销售125.5万辆,同比下降2.3%;SUV销售108.2万辆,同比增长35.6%;MPV销售27.2万辆,同比下降0.5%;交叉型乘用车销售6.4万辆,同比下降32.6%。
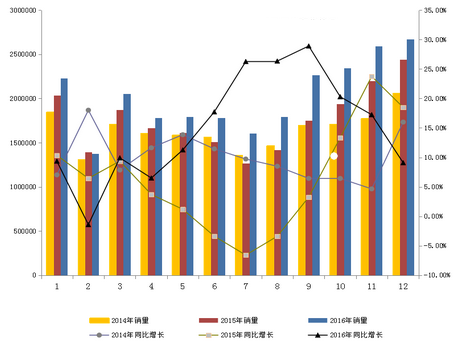
12月商用车生产41.9万辆,环比增长12.4%,同比增长25.1%;销售38.5万辆,环比增长10.5%,同比增长12.1%。
2016年新能源汽车生产51.7万辆,销售50.7万辆,比上年同期分别增长51.7%和53.0%。其中纯电动汽车产销分别完成41.7万辆和40.9万辆,比上年同期分别增长63.9%和65.1%;插电式混合动力汽车产销分别完成9.9万辆和9.8万辆,比上年同期分别增长15.7%和17.1%。
12月新能源汽车生产8.9万辆,销售10.4万辆,同比分别增长16.8%和23.5%。其中纯电动汽车产销分别完成7.7万辆和9.2万辆;插电式混合动力汽车产销均完成1.2万辆。
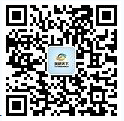
【版权提示】观研报告网倡导尊重与保护知识产权。未经许可,任何人不得复制、转载、或以其他方式使用本网站的内容。如发现本站文章存在版权问题,烦请提供版权疑问、身份证明、版权证明、联系方式等发邮件至kf@chinabaogao.com,我们将及时沟通与处理。