导读:近年国内外冷精锻行业市场需求状况。冷精锻行业发展最为成熟的是日本、美国、德国等工业发达国家。
参考《2017-2022年中国汽车零部件再制造行业竞争现状及十三五竞争策略分析报告》
冷精锻行业发展最为成熟的是日本、美国、德国等工业发达国家,其中以德国和日本钢质零件的冷精锻技术最为发达。它的发展与机动车工业发展息息相关。
1935年,德国开发成功钢材的磷化处理工艺,为钢质零件的冷锻冷挤压成形创造了条件,1955年开始将冷锻技术用于汽车工业。日本汽车工业应用冷锻件在世界上属首位。日本每辆车中冷锻件的数量从1965年的不到5千克上升至到1990年的43千克以上。伴随着机动车用零件的逐步冷锻化,日本冷精锻工艺也在不断发展。由最初生产的简单活塞销、紧固件发展到现在的生产大型高精度等速万向节的外座圈、内座圈、十字轴等高难度冷锻件。
全球平均每辆汽车上机动车工业件的使用量由于不同国家采用不同的归类和统计方法,很难得到完整准确的全球统计数据。一般每辆汽车中冷锻件的用量达40-50千克(数据来源:《挤压技术——金属精密件的经济制造工艺》,(德)K.LangeM.Kammerer著)。据此按照全球汽车产量数据测算,则国内外仅汽车行业对冷锻件需求量测算如下图所示:
2005年至2015年,全球汽车行业对冷锻件需求量呈逐年上升趋势,复合增长率为3.16%。
冷精锻技术在我国规模化生产应用中大致经历了三次发展:20世纪60—70年代,以上海交大为主,将冷精锻技术在我国工程化应用(主要为冷挤压),生产缝纫机、自行车、手表等零部件及少量汽车零件。该阶段冷锻工艺技术水平与国外先进水平差距很大。
20世纪80—90年代,以兵器工业第五九研究所等单位为主,应用于挤压、摆辗、滚轧、精冲等精密塑性成形工艺规模化生产机动车齿类零件。该时期是我国摩托车产业高速发展时期,零部件的国产化刺激了精密冷锻产品的大批量生产;20世纪90年代末至今,我国现代汽车产业迅猛发展,促进了零部件企业工艺技术及工艺装备的同步提升,以国内江浙沪数家精锻公司为主,大量引进国外先进装备及生产线,使得我国的精锻技术水平大幅提高。
目前,冷精锻成形技术已在汽车、电器、军工、航空航天、机械、仪表、轻工、船舶等工业部门中得到较为广泛的应用,已成为金属塑性体积成形技术中不可缺少的重要加工手段之一。
按照我国汽车产量数据测算,我国汽车行业对冷锻件需求量测算如下图所示:
我国汽车行业对冷锻件需求量复合增长率为15.67%,增速明显高于全球水平。此外随着我国行业内技术的进步,我国车身冷锻件的比重也会逐渐增加,也将推动我国汽车行业对冷锻件的需求的增长。
资料来源:公开资料,中国报告网整理,转载请注明出处(YS)。
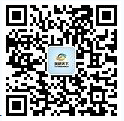
【版权提示】观研报告网倡导尊重与保护知识产权。未经许可,任何人不得复制、转载、或以其他方式使用本网站的内容。如发现本站文章存在版权问题,烦请提供版权疑问、身份证明、版权证明、联系方式等发邮件至kf@chinabaogao.com,我们将及时沟通与处理。