导读:2014年现代航空材料结构无损检测技术现状。要实现复合材料结构高质量的超声扫描成像检测,并非易事,特别是航空复合材料结构,除了如前所述的复合材料自身的不同之处外,另一个非常重要的难题,就是如何解决复杂且变厚复合材料结构的高质量超声可视化成像,尤其对于那些无法实现超声穿透法检测的复合材料结构,更难解决。
按检测对象和应用阶段,现代航空材料和结构无损检测方法可以分为:
①原材料的无损检测。
②轻质金属结构的无损检测。
③复合材料无损检测。
④其他材料与结构无损检测。除了原材料的无损检测,其他检测几乎都是贯穿于航空结构制造、装配与服役全寿命过程。
1 原材料的无损检测
用于原材料的无损检测方法,包括各种航空结构制造用的金属、棒、板材等的无损检测,目前针对这些原材料的无损检测,主要是利用超声检测方法。
其中超声自动扫描检测技术已在金属棒、板材等的超声检测中应用越来越广泛。为了提高检测效率和覆盖材料不同取向的缺陷的检测,多通道检测技术是未来一个重要发展方向。
值得指出的是,在航空应用薄壁管的无损检测中,必须充分考虑到所用超声检测方法和仪器设备的检测灵敏度和分辨率,同时还应考虑缺陷取向和分布特点,检测采用相应的超声覆盖扫查方法,其中利用多通道组成复合扫查方法是一种有效的技术途径。
2 轻质金属结构的无损检测
现代航空产品(这里主要指飞机和发动机)越来越追求减重,所以基于各种轻质合金材料的轻型结构,近年来在飞机和发动机上得到大量推广应用,铝合金和钛合金材料是应用较多的轻质合金材料。基于这些轻质材料航空结构的无损检测,至少包括固相焊接结构无损检测、特种焊接结构的无损检测和其他轻质金属结构的无损检测。
2.1 固相焊接无损检测
目前在航空领域得到应用的固相焊接结构,主要包括基于扩散焊、搅拌摩擦焊和线性摩擦焊等新型焊接工艺的固相焊接结构。首先,由于固相焊接工艺及其焊缝区可能产生的焊接缺陷与传统熔焊具有迥然不同的物理和冶金组织特征;其次,不同固相焊接工艺彼此的特点不同;第三,固相焊接焊缝区缺陷具有明显的紧贴细化、取向复杂等特点。因此,固相焊接结构的无损检测方法选择,首先必须跳出熔化焊焊缝检测的理念,例如,在良好焊接情况下,固相焊接(如扩散焊)其冶金组织与母材一致,没有明显的焊缝区。
某企业研究的高分辨率超声检测方法、超声PUDE检测方法、超声变入射角检测方法和检测仪器以及建立的固相焊接缺陷判别方法,一直在航空领域得到十分重要的应用。
例如,上图是采用脉冲回波超声衍射法PUDE(Pulsed Ultrasonic Diffraction Echoes)在铝合金搅拌摩擦焊缝中检出的实际焊接缺陷,如图中指示的浅颜色分布区所示。而采用X-射线和常规超声检测方法均没有能够检出该缺陷。这主要是缺陷具有紧贴和复杂取向特点的原因。
上图是采用高分辨率超声扫描成像方法在钛合金扩散焊中检出的实际弥散未焊合缺陷,如图白色 灰 度 分 布 所 示,成 像 区 域 大 小 为10 mm×10mm。同样,采用X-射线和常规超声检测方法均未能检出该缺陷。这主要是由于该缺陷具有紧贴和微细的特点。
2.2 特种焊接结构的无损检测
目前在航空领域得到推广应用的特种焊接工艺,主要包括钎焊、TLP扩散焊、激光焊、电子束焊等。基于这些特征焊接工艺的特种焊接结构,主要用于飞机和发动机结构的制造。因其结构较为复杂,目前较为可行的无损检测方法主要是采用X-射线和超声两种检测方法。
某企业通过试验使用非线性超声成像和超声LTOFD等检测方法,显著地提高了特种焊接缺陷检测能力和超声对特种焊接缺陷的检测能力,已经取得了很好的检测效果。
2.3 其他轻质结构的无损检测
轻质结构还有一种制造方法,就是采用传统的机械加工方法成型。这种轻质结构通常在成型后都具有较为复杂的几何外形,内部缺陷的检测更要严格执行原材料无损检测进行把关。后序的加工成型过程中,则主要是采用渗透、涡流、超声等检测方法,检测这类结构在后序机械加工或者热处理过程中可能产生的表面和近表面缺陷。
2.3 复合材料无损检测
在国际上也有将复合材料归类为轻质材料结构。由于复合材料与金属材料有着十分不同的内部微结构差异和成型工艺,因而复合材料的无损检测一直是无损检测领域的一个专门的研究和应用方向,特别是近20a来复合材料在航空领域呈现突飞猛进的扩大应用势头,在有些飞机型号上的应用甚至超过飞机结构重量的50%以上。
复合材料没有中间加工过程,从结构零件的铺层制备到成型,通常只需要一个热循环过程完成。复合材料结构本身也没有厚度方向的加工余量,加上其内部呈现多界面物理结合状,因此,复合材料无损检测与缺陷判别方法、检测要求、检测环境、检测认知、检测理念、检测仪器设备都与传统金属材料的无损检测相差甚远。
通常需针对复合材料结构特点,试验和制定有效的无损检测方法,建立复合材料结构专用检测仪器设备、检测方法规范。复合材料无损检测首先需考虑检测的分辨率、表面检测盲区、检测灵敏度以及缺陷检出能力与可检性;其次,必须考虑到复合材料无损检测与缺陷判别的显著差异。
从技术层面上,目前用于复合材料的无损检测方法主要有超声、X射线、声振(声阻)、激光电子剪切、红外等,其中超声检测方法的应用最为成熟和广泛。
3.1 超声检测技术
超声是目前针对复合材料结构的一种主要无损检测方法。目前国际上70%~80%以上的复合材料结构都采用了超声检测方法。与金属材料相比,复合材料微结构及制造工艺、结构特征等迥然不同,故必须采用专门的复合材料无损检测技术,包括超声检测实现方法、检测仪器设备、检测工艺规范、缺陷判据与识别方法等。必须有效解决复合材料超声检测的分辨率和表面检测盲区,通常要求达到单个复合材料铺层厚度(hi)。对复合材料层压结构,hi≈0.13mm,其中重要且有效的技术途径是使超声检测回波信号特性达到单周。
图 复合材料高分辨率超声C扫描结果图
上图是采用通过高分辨超声检测方法和设备,对一位于两个铺层之间的碳纤维复合材料分层的超声C扫描结果,此处复合材料厚度为2hi≈0.26mm,缺陷的深度hi≈0.13mm,缺陷大小为12.5mm分层,从图中可以清晰看出分层缺陷的大小和分布,展现出了很好的检测分辨率。
对航空领域大量采用的复合材料结构,必须考虑能实现工程结构件的100%扫查覆盖,尤其是解决大型复合材料结构的高效超声自动扫描可视化成像检测。因此,目前大型复合材料结构的超声无损检测已成为国际上复合材料领域的一个十分重要的支撑技术和发展方向。
要实现复合材料结构高质量的超声扫描成像检测,并非易事,特别是航空复合材料结构,除了如前所述的复合材料自身的不同之处外,另一个非常重要的难题,就是如何解决复杂且变厚复合材料结构的高质量超声可视化成像,尤其对于那些无法实现超声穿透法检测的复合材料结构,更难解决。某企业经过20多年的持续试验研发,近年在面向复合材料结构高效超声自动扫描可视化成像方面,取得了非常骄人的自主研发成果和工程应用效果。
下图是某企业自主研制,且列装投入规模化生产应用的工业级大型复合材料结构高效超声自动扫描成像系统,检测效率比传统超声检测方法提高近20倍,有效检测范围可达6m×9m以上,具有独特的曲面自适应跟踪能力,也是继波音和空客之后的又一面向工业级的大型复合材料结构高效自动扫描成像检测系统,其中CUS-6000、MUI-2000等都是这方面非常有效的检测设备。
大型复合材料结构高效超声自动扫描成像检测系统
3.2 X射线检测技术
X射线检测技术包括基于DR和CT以及胶片照相等检测方法。
X射线方法主要是在高温复合材料、复合材料夹层结构的缺陷检测,泡沫填充区的检测方面有一定效果,总体上X射线不适合用于复合材料蒙皮、壁板等大多数复合材料结构的大面积检测。而很多的时候也难以有效检测复合材料结构呈现层间分布特点的缺陷。
3.3 声振(声阻)检测
这种方法最大的优点是点接触耦合,廉价快捷,是目前复合材料胶接结构的一种非常廉价有效的检测方 法,特 别 是 外 场 检 测 和 修 理 检 测,其 中 的Z2000、DAMI-C都是在这方面非常有效的检测仪器,而且是目前在工程上一直得到广泛应用的复合材料胶接检测仪器。声振检测方法不适合检测复合材料层压结构内部缺陷。
3.4 激光电子剪切成像方法
电子剪切成像方法是在传统激光散斑基础上发展起来的一种更为直观、可视化的检测方法,采用单束光干涉,对环境和隔振要求大大降低,同时具有面积扫描和非接触特点,但仍需要加载,而且只有对那些因缺陷的存在,能够在外加负载作用下产生表面可检测到的变形或位移的应用场合才适用。因此,激光电子剪切成像在一些复合材料夹层结构、胶接结构等方面有一定的适用性。下图是某企业研发的电子剪切成像仪在复合材料橡胶胶接结构方面的应用实例,从图中3D成像检测结果中可以更清晰、形象、直观地看到这些小气孔和气孔群及其分布,获得了较好的工程应用效果。
实际胶接工艺缺陷的激光电子剪切3D成像检测结果
3.5 其他检测方法
随着多种复合材料的研发与应用,以及外场环境条件下检测要求,红外(包括THz)、激光超声、超声显微等近年来也不断地得到发展,针对一些特定的复合材料应用案例和检测对象,目前也有了一定的验证试验和初步应用,但要达到面向复合材料工程结构的无损检测技术层面,还尚需今后从技术上不断试验、沉淀和积累以及支撑技术的发展。
《中国航空材料行业产销分析及投资趋势分析报告(2013-2017)》由中国报告网航空材料行业分析专家领衔撰写,主要分析了航空材料行业的市场规模、发展现状与投资前景,同时对航空材料行业的未来发展做出科学的趋势预测和专业的航空材料行业数据分析,帮助客户评估航空材料行业投资价值。
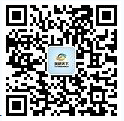
【版权提示】观研报告网倡导尊重与保护知识产权。未经许可,任何人不得复制、转载、或以其他方式使用本网站的内容。如发现本站文章存在版权问题,烦请提供版权疑问、身份证明、版权证明、联系方式等发邮件至kf@chinabaogao.com,我们将及时沟通与处理。