导读:航空零部件精密加工技术:数控加工技术与特殊过程工艺处理。航空零部件结构、形状、各零部件间配合关系复杂,部分零部件存在大量薄壁,而用于航空零部件加工的材料主要为航空特殊铝合金、钛合金及不锈钢等材料,其材质轻难加工,且本身尺寸跨度大,很容易发生变形,因此,在航空零部件的制造中,数控加工技术得到普遍应用。根据零部件本身的特点决定采用何种加工方法和装备。
参考《2017-2022年中国通用航空市场运营态势及十三五盈利战略分析报告》
数控加工技术、特殊过程工艺处理等是航空零部件精密加工的关键技术。
1、数控加工技术
航空零部件结构、形状、各零部件间配合关系复杂,部分零部件存在大量薄壁,而用于航空零部件加工的材料主要为航空特殊铝合金、钛合金及不锈钢等材料,其材质轻难加工,且本身尺寸跨度大,很容易发生变形,因此,在航空零部件的制造中,数控加工技术得到普遍应用。根据零部件本身的特点决定采用何种加工方法和装备。形状较简单的结构件,采用三轴或四轴数控机床就可以进行加工;形状复杂的结构件,受刀具与零件相对位置的限制,采用三轴或四轴数控机床则需要多次装卡才能完成零件的加工。而每增加一次装夹,就增加一次误差来源,从而影响零件最终精度,并增加加工时间。同样受刀具与零件相对位置的限制,技术编程人员必须极其小心的避免刀具与零件的干涉,而且通常很难利用刀具最佳的切削位置,切削效率降低。由于复杂零件工艺要求高、加工难度大以及耗时长等原因,一般选择采用五轴数控联动机床加工。由于五轴数控联动机床有两个旋转轴,刀具与零件的相对位置更为灵活,其加工方式可以实现在一次装夹条件下对零件进行整体加工,刀具能够以理想的角度接近切削表面,实现最佳切削。五轴联动加工技术是现代航空零部件数控加工的发展趋势。但由于目前国内高端五轴联动数控机床主要依靠进口,且单价远高于三轴、四轴数控联动机床,大量使用五轴联动数控机床将直接导致生产成本的提高,因此,加工企业通常仅采购必要的五轴联动数控机床加工部分形状复杂的结构件。
基于数控加工技术,相应还需要成熟稳定的加工工艺及技术予以配合,才能满足零部件机加成型要求。比如:高精度盲孔加工技术、复杂深腔钛合金类零件加工技术、复杂薄壁类零件多面加工技术、热成型技术、表面完整性机械加工与智能控制技术等。
2、特殊过程工艺处理
特殊过程工艺处理主要包括无损检测、热处理、表面处理等。
无损检测为航空零部件制造过程中非常重要的环节。飞机结构制造的主要任务是通过制造平台、利用给定的加工工艺和工艺文件,将材料加工成图纸设计要求的飞机结构或零件,在此过程中无损检测的主要作用就是确保每道工序的制造质量符合设计要求,及时发现结构制造过程中可能产生的超标缺陷,不让前一道制造工序产生的缺陷带到后一道制造工序。
热处理工艺一般包括加热、保温、冷却等工序。由于航空零部件加工材料主要为金属材料,其材料自身会存在一定的内应力,通过机械加工后的零部件会加大材料内应力,内应力突破界限将使零部件产生裂纹,导致产品质量问题,因此,航空零部件产品出厂都要求达到零应力状态。为此,就需要对零部件半成品或成品进行热处理,以改变力学性能、物理性能和化学性能,并消除内应力。
此外,航空产品需要在恶劣环境中自主完成各种任务,要求其零部件具有良好的耐高温和低温性能、良好的抗老化和腐蚀性能力,以及较强的断裂韧性和抗疲劳性能,用以保证其可靠性和安全性。为此,就需要对零部件半成品进行高品质的强化和表面处理。比如:阳极化处理可在铝材等表面形成厚度适宜的氧化膜,显著提升零部件的耐蚀性、硬度、耐磨性、绝缘性和耐热性,如再经热水、高温水蒸气或镍盐封闭处理后,则其耐蚀性和耐磨性还能进一步得到提高;喷丸强化在一个完全控制的状态下将无数小钢丸高速且连续喷射,捶打到零件表面,从而在表面产生一个残余压应力层,零件在压应力层保护下,极大程度地改善了抗疲劳强度,并可防止零部件变性,延长安全工作寿命。
目前国内航空制造领域特殊过程工艺处理产能绝大多数集中在国有大型企业,公司拟通过募投项目完善此业务环节。
资料来源:公开资料,中国报告网整理,转载请注明出处(YS)。
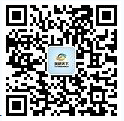
【版权提示】观研报告网倡导尊重与保护知识产权。未经许可,任何人不得复制、转载、或以其他方式使用本网站的内容。如发现本站文章存在版权问题,烦请提供版权疑问、身份证明、版权证明、联系方式等发邮件至kf@chinabaogao.com,我们将及时沟通与处理。