导读:近几年我国合成氨技术发展水平分析,近几十年来,我国合成氨技术取得了重大进展,尤其是单系列流程优化、降低能耗以及设备制造技术的进步,促使合成氨生产技术发展到一个新的阶段。近年来,国内合成氨行业平均能耗呈逐年降低趋势,行业内部不间断的技术改造也促成了能耗的进一步降低。
20世纪70年代由于发生了世界范围的能源危机,国外各公司为了提高在合成氨领域的竞争力,纷纷推出节能型新工艺。到20世纪80年代,以天然气为原料的大型合成氨装置吨氨能耗降至29.30GJ左右;到20世纪90年代,以煤为原料的大型合成氨装置吨氨能耗降至46.05~50.24GJ。
近几十年来,我国合成氨技术取得了重大进展,尤其是单系列流程优化、降低能耗以及设备制造技术的进步,促使合成氨生产技术发展到一个新的阶段。近年来,国内合成氨行业平均能耗呈逐年降低趋势,行业内部不间断的技术改造也促成了能耗的进一步降低。2011年我国天然气转化生产合成氨的吨氨平均能耗折合标准煤耗为1259kg(36.90GJ),固定层间歇式煤气化生产合成氨吨氨的平均能耗折合标准煤耗为1436kg(42.09GJ),采用加压煤气化的合成氨吨氨平均能耗折合标准煤耗为1450~1650kg(42.50~48.36GJ)。
“十一五”期间,我国合成氨原料结构调整取得了重大进展。目前原料结构比例为煤炭占74.6%,天然气占24.4%,重油占0.4%,焦炉气占0.6%。
我国现有1000t/d以上的大型天然气合成氨生产装置共27套,总生产能力900万t/a,占全国合成氨总产能的13.7%。这些装置是20世纪70年代以来先后引进的,其中早期引进的装置,多数进行了技术改造。这些装置的技术水平基本上都达到了国际先进水平。目前,具有我国自主知识产权的20万t/a天然气制氨装置已建成投产,其技术水平基本与引进的大型装置相当。
到2011年底,全国采用连续煤气化技术生产合成氨的企业共29家,合计生产能力820万t/a,占全国合成氨总产能的12.3%。其中,以多喷嘴对置式水煤浆气化技术、HT-L航天粉煤加压气化技术、经济型气流床分级气化技术为代表的一批拥有自主知识产权的煤气化技术研制成功,并投入工业运行,是我国氮肥工业技术进步取得的重大突破,为“十二五”期间氮肥工业实现装置大型化奠定了基础。
观研天下在《中国合成氨产业全景调研与发展趋势研究报告(2013-2017)》中提到,“十一五”期间,合成氨生产中一些关键部位的技术水平也普遍提高。特别是氨合成原料气精脱硫、低水/汽比变换、醇烃化精制工艺、两段法变压吸附、大型(千吨级)径向氨合成等多项技术,具有自主知识产权,并达到了国际先进水平。
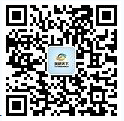
【版权提示】观研报告网倡导尊重与保护知识产权。未经许可,任何人不得复制、转载、或以其他方式使用本网站的内容。如发现本站文章存在版权问题,烦请提供版权疑问、身份证明、版权证明、联系方式等发邮件至kf@chinabaogao.com,我们将及时沟通与处理。