润滑油是用在各种类型汽车、机械设备上以减少摩擦,保护机械及加工件的液体或半固体润滑剂,主要起润滑、辅助冷却、防锈、清洁、密封和缓冲等作用(Roab)。
参考观研天下发布《2018年中国润滑油行业分析报告-市场运营态势与发展前景研究》
一、中国润滑油行业现状
据不完全统计,截至2017年底,中国润滑油市场需求量为530万吨(不含白油、橡胶油、防冻液等),同比增长1.9%。从近几年市场需求量看,中国润滑油行业已进入平稳发展期,稳增长的动能和潜力正在积聚,未来润滑油产业结构和发展质量必将得到进一步的优化提升。
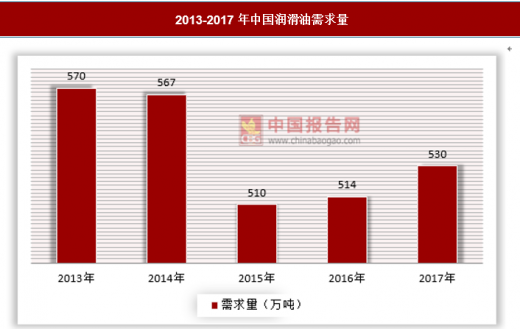
二、中国润滑油行业竞争格局
2017年中国润滑油行业竞争格局如下,国内润滑油行业主要有三类,第一类是国企,即中石油和中石化,市场份额约为50%;第二类是地方民企,占比25%;第三类为跨国公司,占比为25%。
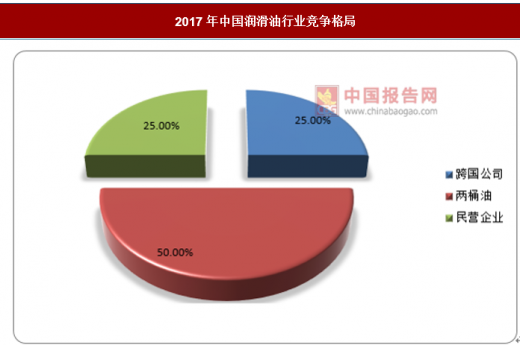
企业部分,目前国内实力排名靠前的润滑油制造企业为昆仑润滑油和长城润滑油,其次是民企的玉柴润滑油公司和舜能润滑油公司。目前国内拥有润滑油企业约2,000余家,其中中小企业数量多、规模小、抗风险能力差,行业竞争激烈。同时,外资润滑油公司凭借领先的技术及综合实力,在竞争中占据有利地位。
三、废润滑油
废润滑油主要产生于机动车维修保养和拆解过程以及工业企业生产加工过程中,是废矿物油中典型的一类废油,属于我国《国家危险废物名录》中HW08废矿物油与含矿物油废物类别,其中含有多种有毒有害物质,如重金属、苯系物、多环芳烃等,直接丢弃会造成水体和土壤污染,破坏生物的正常生活环境,并对其造成生物机能障碍的作用。另一方面,废润滑油具有较高的再生利用价值,可以通过适宜的再生技术再生为基础油、燃料油和柴油等产品。我国石油资源不足,原油对外依存度超过65%,而废润滑油再生利用可直接节约石油资源。据统计,2015年我国废矿物油产生总量达到3000万t,保持年3%的稳定增长速度,到2020年其产量预计超过3500万t,其中废润滑油产生量约为500万t,废润滑油再生利用具有巨大潜力。
四、典型废润滑油再生技术
目前国内对废润滑油的再生利用工艺主要有白土高温接触无酸再生工艺、蒸馏-糠醛精制-白土精制工艺、高温蒸馏工艺、溶剂精制工艺、薄膜蒸发、膜过滤法、蒸馏-加氢工艺等。国外废润滑油再生技术主要有Kleen、Meinken、IFP、KTI、Snamprogetti、DOH、DCH、BERC和Recyclon工艺等,已经获得应用的新工艺还有超滤、离心分离、分子蒸馏、絮凝处理、溶剂精制、蒸馏-加氢等。
1、沉淀处理工艺
沉淀法利用水分、机械杂质不溶于油,且密度大于油的特点,采用物理的方法降低黏度等手段,将其从油中分离出来。由于废润滑油黏度较大,一般将其倒入加温沉淀设备中,加热到70~80℃后静置,加热的目的是降低废润滑油的黏度,使废润滑油中的水分、杂质沉降速度加快。加热最高温度一般不宜超过90℃,否则废润滑油会快速氧化,超过100℃会使油液中的水分沸腾,影响沉淀过程,由于润滑油的黏度在80℃随温度变化最大,超过则变化变缓,一般沉降温度在70℃左右为宜。沉淀法只能去除废润滑油中的部分水分和杂质,不能解决油液中酸性升高及氧化等问题。
2、溶剂精制工艺
溶剂精制是一种物理分离过程,依据的原理为利用溶剂活性极性分子的选择性溶解能力,溶解废润滑油中非理想成分(如氧化物和金属化合物),并将其分离出来。溶剂精制中常用的溶剂有糠醛、苯酚和NMP。溶剂精制工艺使用的设备价廉且操作简便,溶剂无毒,可以多次回收利用,其精制得到的润滑油收率高,品质较好。溶剂精制可分为单一溶剂精制和复合溶剂精制,单一溶剂精制中,NMP具有低挥发性,无毒,对不饱和烃、芳香烃和硫化物溶解性和选择性强等特点,是良好的萃取芳香烃的溶剂。复合溶剂精制采用2种或以上溶剂按照一定比例进行混合,基于之间的缔合作用等,可明显改善非理想组分的萃取效果。此外,还可以添加适宜的有机或无机絮凝剂,以达到更好的再生效果。
3、蒸馏工艺
蒸馏是废润滑油再生过程中较为关键的一步。常压蒸馏主要用于脱除废机油的水分、汽油或柴油。减压蒸馏主要是脱除废润滑油中的沥青质、胶质、添加剂、金属盐等或用于切割基础油馏分,而且多通入水蒸气,即采用水蒸气蒸馏。废润滑油再生装置采用高真空和更低的温度,可避免润滑油馏分的热分解。薄膜蒸发法,是在真空度约500Pa的条件下,使被蒸馏的液体向下流动,经过加热的筒壁表面分散成为薄的快速运动的薄膜。其具有温度低、停留时间短和蒸发量大的优点,根据薄膜分散方式不同,可分为擦膜蒸发器、旋风式薄膜蒸发器、固定浆间隙薄膜蒸发器,其中,前2种在废润滑油再生中应用较多。分子蒸馏技术又称短程蒸馏,其具有蒸馏温度低、蒸馏时间短、蒸发效率高、分离程度高、降低高沸点的物料分离成本等优点。分子蒸馏装置具有高效传热传质的特点,其对处理物料的要求也是相当苛刻,因此在采用分子蒸馏处理废润滑油时一般要经过预处理去除机械杂质等污染物。
4、加氢工艺
典型蒸馏-加氢工艺技术可简述如下:1)预处理。废润滑油进入闪蒸塔去除其中的水和轻沸物,之后进入蒸馏塔中分馏为2或3个部分,汽油在塔顶被分馏。2)催化加氢。润滑油馏分与氢气充分混合,进入加氢精制反应器中,该步骤去除预处理中未能完全去除的金属,也起到初步脱硫的作用,同时催化剂与润滑油的烯烃键分子和芳香烃键分子充分接触,使加氢反应快速进行,起到完全脱硫脱氮的作用。3)将加氢反应产物进行闪蒸,从塔顶分离出的未反应氢气及酸性气进入洗涤罐,氢气被洁净后循环使用;从塔底分离出的精制润滑油被送入汽提-干燥系统,经进一步脱除酸性气后,得到精制润滑油基础油。该工艺的产品收率高、质量好,但设备投资高,操作较复杂,且加氢条件苛刻,需要合适的氢气来源。反应温度不得高于250℃,加氢成本高,不适合小规模处理。
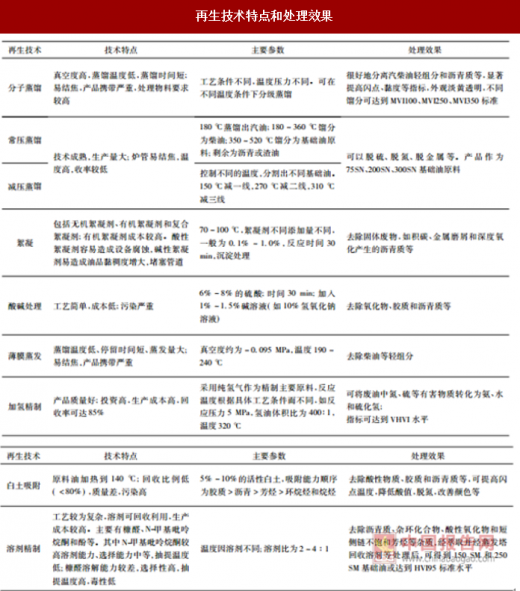
截至2017年6月持有废矿物油与含矿物油废物经营许可证的企业共412家,其中企业数量较多省份分别是广东省、江苏省、山东省和浙江省等。对各企业废润滑油处理中间环节和精制阶段采用的技术分布情况进行分析得到,中间处理环节采用常压蒸馏、减压蒸馏(精馏)的企业最多,占47%。有超过50%的企业没有精制工艺,采用溶剂精制的企业最多,占26%。
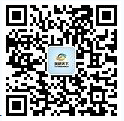
【版权提示】观研报告网倡导尊重与保护知识产权。未经许可,任何人不得复制、转载、或以其他方式使用本网站的内容。如发现本站文章存在版权问题,烦请提供版权疑问、身份证明、版权证明、联系方式等发邮件至kf@chinabaogao.com,我们将及时沟通与处理。