镍基高温合金是高温合金中应用最广、高温强度最高的一类合金。
其主要原因,一是镍基合金中可以溶解较多合金元素,且能保持较好的组织稳定性;二是可以形成共格有序的A3B型金属间化合物[Ni3(Al,Ti)]相作为强化相,使合金得到有效强化,获得比铁基高温合金和钴基高温合金更高的高温强度;三是含铬的镍基高温合金具有比铁基高温合金更好的抗氧化和抗燃气腐蚀能力。
可以说,镍基高温合金的发展决定了航空涡轮发动机的发展,也决定了航空工业的发展。采用定向凝固技术制备出的镍基单晶合金,其使用温度已接近合金熔点的90%,成为当代先进航空发动机热端部件不可替代的重要结构材料。
镍基高温合金含有十多种元素,添加合金元素对高温合金的性能起关键的作用。
以铸造镍基高温合金为例,铸造镍基高温合金以γ相为基体,添加铝、钛、铌、钽等形成γ’相进行强化,γ’相数量较多,有的合金高达60%;加入钴元素能提高γ’相溶解温度,提高合金的使用温度;钼、钨、铬具有强化固溶体的作用,铬、钼、钽还能形成一系列对晶界产生强化作用的碳化物;铝、铬有助于抗氧化能力,但铬降低γ’相的溶解度和高温强度,因此铬含量应低些;铪改善合金中温塑性和强度;为了强化晶界,添加适量的硼、锆等元素。
研究表明,GMR235铸态合金的含碳量为0.18%时,高温持久寿命和抗拉强度最大,且具有较好的塑性,添加硼和锆的合金持久性明显改善,合金的枝晶间距减少,碳化物的析出量减少且碳化物颗粒细化,从而改善各方面性能。
镍基高温合金是20世纪30年代后期开始研制的。英国于1941年首先生产出镍基高温合金Nimonic75;为了提高蠕变性又添加了铝,研制出Nimonic80。美国于40年代中期,苏联于40年代后期,中国于50年代中期也研制出镍基合金。
镍基合金的发展包括两个方面:合金成分的改进和生产工艺的革新。
50年代初,真空熔炼技术的发展,为炼制含高铝和钛的镍基合金创造了条件。初期的镍基合金大都是变形合金。
50年代后期,由于涡轮叶片工作温度的提高,要求合金有更高的高温温度,但是合金的强度高了,就难以变形,甚至不能变形,于是采用熔模精密铸造工艺,发展出一系列具有良好高温强度的铸造合金。
60年代中期发展出性能更好的定向结晶和单晶高温合金以及粉末冶金高温合金。
为了满足舰船和工业燃气轮机的需求,60年代以来还发展出一批抗热腐蚀性能较好、组织稳定的高铬镍基合金。在从40年代初到70年代末大约40年的时间内,镍基合金的工作温度从700℃提高到1100℃,平均每年提高10°C左右。
镍基高温合金按照制造工艺,可分为变形高温合金、铸造高温合金、粉末冶金高温合金。
1变形高温合金
变形高温合金是高温合金中应用最广的一类,占比达到70%。
变形高温合金主要采用常规的锻、轧和挤压等冷、热变形手段加工成材。我国镍基变形高温合金以拼音字母GH加序号表示,如GH4169、GH141等。
变形高温合金塑性较低,变形抗力大,使用普通的热加工手段变形有一定困难,因而需要采取钢锭直接轧制、钢锭包套直接轧制和包套墩饼等新工艺来加工,也采用加镁微合金化和弯曲晶界热处理工艺来提高塑性。
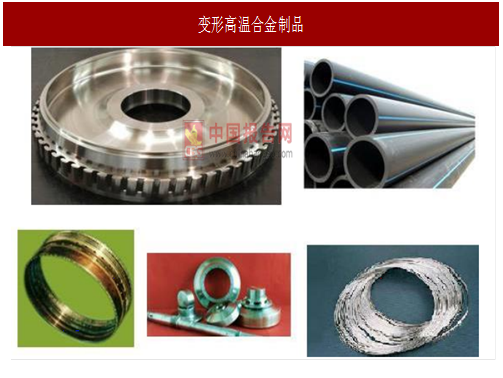
变形高温合金在航空发动机中至今仍然是主要用材。
其中GH4169在我国航空发动机中已得到广泛应用,被称为高温合金中的万金油。其材质水平和加工工艺水平近年来得到显著提高。GH4169合金的冶金产品有不同规格的锻棒、热轧棒、冷拉棒、板、带、丝、管和锻件,制造的零件有各类盘、转子、环、机匣、轴、紧固件、弹性元件、阻尼元件等。
据《变形高温合金GH4169》(庄景云等),文献《镍基高温合金的研究现状与发展前景》(2014.01),该材料在发动机中的用量已由几个、十几个零件号增加至二百多个,如我国三代战机主力发动机太行(即涡扇10)中应用GH4169合金的零件号达261个,零件总质量占核心机质量的60%,占发动机质量的30%以上。
GH4169合金制造的最重要的零件就是航空发动机用涡轮盘。在太行发动机中,仅盘件就多达11种之多。近几年,国产盘锻件的组织性能达到了较高水平,每年生产昆仑发动机(涡喷14)、太行发动机用盘锻件1000余件。此外,该合金在大飞机发动机和直升机发动机用涡轴系列发动机中也获得广泛应用。
2铸造高温合金
随着使用温度和强度的提高,高温合金的合金化程度越来越高,热加工成形越来越困难,必须采用铸造工艺进行生产。
另外,采用冷却技术的空心叶片的内部复杂型腔,只能采用精密铸造工艺才能生产,因此镍基铸造高温合金在实际生产应用中不可缺少。铸造高温合金应用也较为广泛,占比约20%。国内的铸造高温合金以“K”加序号表示,如K1、K2等。
按结晶方式,铸造高温合金又可以分为多晶铸造高温合金、定向凝固铸造高温合金、定向共晶铸造高温合金和单晶铸造高温合金等4种类型。
铸造高温合金的特点是:
1)具有更宽的成分范围。由于不必兼顾变形加工性能,合金的设计可以集中考虑优化其使用性能。
2)具有更广阔的应用领域。由于铸造方法具有的特殊优点,可根据零件的使用需要,设计、制造出近终型或无余量的具有任意复杂结构和形状的高温合金铸件。
根据铸造合金的使用温度,可以分为三类:
1)在-235-650℃使用的等轴晶铸造高温合金。这类合金在很大温度范围内具有良好的综合性能,特别是在低温下能保持强度和塑性均不下降。如在航空、航天发动机上用量较大的国产K4169合金,其650℃拉伸强度为1000MPa、屈服强度850Mpa、拉伸塑性15%;650℃,620Mpa应力下的持久寿命为200小时。已用于制作航空发动机中的扩压器机匣及航天用液体火箭发动机中各种泵用复杂结构件等。
2)在650℃~950℃使用的等轴晶铸造高温合金。这类合金在高温下有较高的力学性能和抗热腐蚀性能。例如国产K419合金,950℃时,拉伸强度大于700Mpa、拉伸塑性大于6%;950℃、200小时的持久强度极限大于230Mpa。这类合金适用于航空发动机涡轮叶片、导向叶片及整铸涡轮。
3)在950℃~1100℃使用的定向凝固柱晶和单晶高温合金。这类合金在此温度范围内具有优良的综合性能和抗氧化、抗热腐蚀性能。例如国产DD402单晶合金,1100℃、130Mpa的应力下持久寿命大于100小时。这是国内使用温度最高的涡轮叶片材料,适用于制作新型高性能发动机的一级涡轮叶片。
‘
3粉末冶金高温合金
随着耐热合金工作温度越来越高,合金中的强化元素也越来越多,成分也越复杂,导致一些合金只能在铸态上使用,不能够热加工变形。
并且合金元素的增多使镍基合金凝固后成分偏析严重,造成组织和性能的不均匀。采用粉末冶金工艺生产高温合金就能解决上述问题。
因为粉末颗粒小,制粉时冷却速度快,消除了偏析,改善了热加工性,把本来只能铸造的合金变成可热加工的形变高温合金,屈服强度和疲劳性能都有提高,粉末高温合金为生产更高强度的合金产生了新的途径。目前国内粉末高温合金已应用于先进型号发动机上的涡轮盘、压气机盘等重要部件上。
粉末高温合金的工艺流程大致为:预合金粉末制造-压实(热压、热等静压、挤压等)-热加工变形(轧制、模锻等)-热处理。
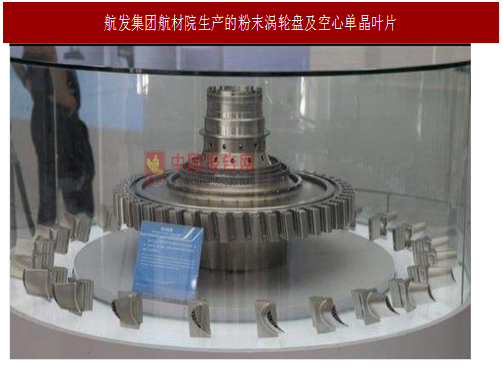
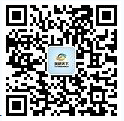
【版权提示】观研报告网倡导尊重与保护知识产权。未经许可,任何人不得复制、转载、或以其他方式使用本网站的内容。如发现本站文章存在版权问题,烦请提供版权疑问、身份证明、版权证明、联系方式等发邮件至kf@chinabaogao.com,我们将及时沟通与处理。