在 LED 显示领域,随着上游封装技术的发展,行业内已逐步形成了 LAMP、SMD 以及 COB 三种不同的 LED 显示面板制备工艺。LAMP 工艺主要用于大间距 LED 显示产品,小间距 LED 显示产品可通过 SMD 或 COB 工艺进行生产。
SMD 采用表贴技术封装 LED 产品,将灯杯、支架、晶元、引线、环氧树脂等材料封装成不同规格的灯珠,再用高速贴片机,以高温回流焊将灯珠焊在电路板上,制成不同间距的显示单元。由于 SMD 在封装阶段的技术难度较低,成为小间距 LED 显示产品的最早路线选择,目前市场上像素间距小于 2.5mm 的 LED 显示产品的生产以 SMD 工艺为主。
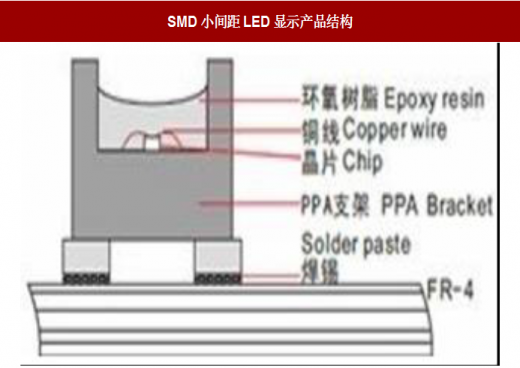
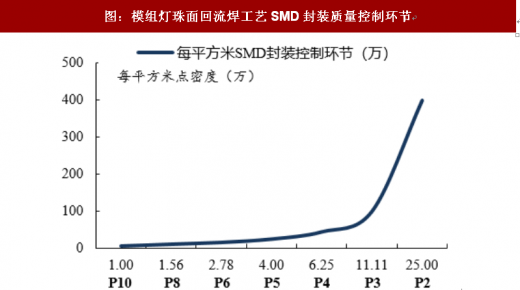
随着 LED 小间距显示市场的快速增长,SMD 分立器件小间距 LED 显示屏在应用中逐渐暴露出技术瓶颈与局限性,主要包括:1)可靠性与稳定性问题,较高的失效率使得维修成本大幅提高;2)点间距的局限,目前主流点间距在 P1.2-P2.0 之间,几乎没有 P1.0 以下间距量产的产品;3)脆弱的防护性,采用 SMD 封装器件,由于灯珠焊盘面积太小,SMT 回流焊后,PCB 板上的灯珠非常脆弱,搬运、安装、使用中的磕碰极易损坏灯珠;4)存在点光、眩光以及重影的问题;5)随着产品点密度的增加,贴片技术难度增加,产品成本也随之增加,且呈非线性加快增长关系。
为了解决 SMD 分立器件小间距显示屏技术路线的瓶颈,业界提出了 COB(Chip On Board)封装小间距显示屏技术路线,即将 LED 芯片直接固晶焊线在带显示电路 PCB 板上,再用封装胶对 LED 芯片包封。

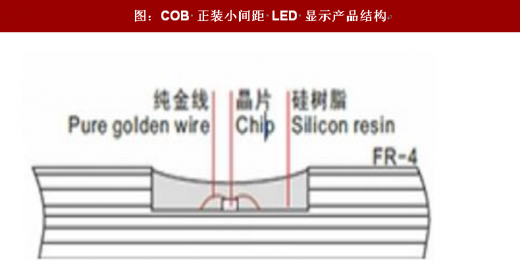
与 SMD 分立器件 LED 显示技术相比,COB 技术具有明显的优势,主要包括:
1) 高可靠性:采用 COB 封装工艺的全彩屏死灯率小于十万分之五,单、双色屏小于百万分之八,远低于 LED 显示屏行业万分之三的标准。
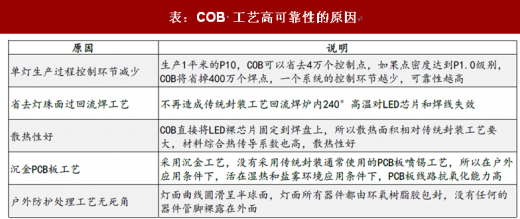
2) 节省成本:COB 封装不再使用支架和编带等金属原材料,节省原材料成本;省去支架重量,而 1 平米的 SMD P3 全彩屏会用到 111111 个支架,同时用胶量很少,1 块 1024 个灯珠的 P3 全彩模组用胶量不到 3 克,进而节省物流成本;省去灯珠线路板的切割、分光、编带和灯面的回流焊工艺,节省工序加工成本;整合 LED 产业链的中、下游企业,1 个企业就可实现从 LED 灯珠的封装到显示屏的制作,节省生产组织成本、中间环节的包装和物流成本、质量控制成本等。
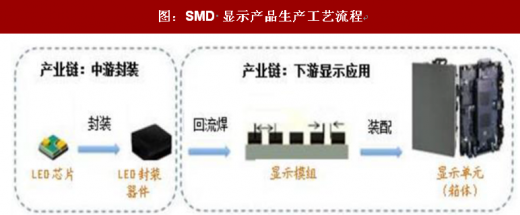
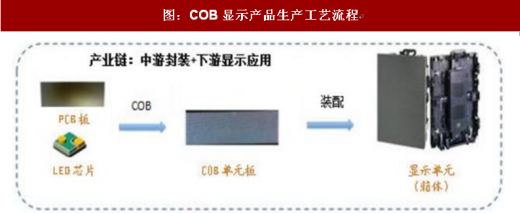
3) 易于实现小点间距:从物理空间尺寸来看,COB 封装在设计灯珠直径时不再受制于支架尺寸的限制,能做到更小的 P0.5-P2.0 点间距,覆盖 SMD 技术难以量产的 P1.0 以下的市场。
4) 更强的物理特性:轻薄,COB 封装模组的重量比 SMD 轻 1/2,以点密度相同的户外模组对比,COB 每平米比 SMD 轻 5-10kg;大视角,采用半球面透镜发光,没有面盖遮挡,发光角度可达 180°,而 SMD 一般在 125°左右;易弯曲,由于 COB 没有支架焊接,LED 芯片由环氧树脂胶密封在灯位内,是可以任意弯曲的;画质的均匀性、色彩曲线、可视角度效果等显著提高;此外,COB 还具备抗压、耐冲击、耐磨、易清洗等优势。
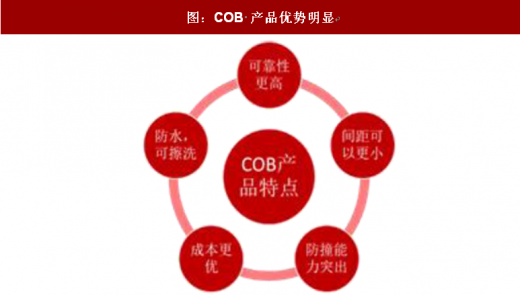
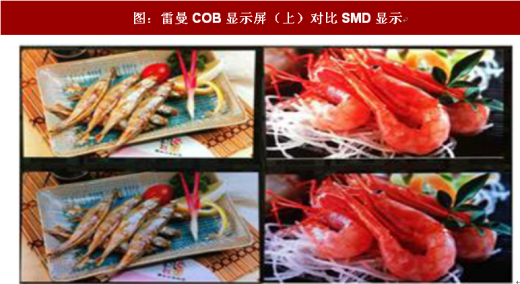
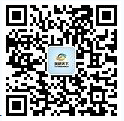
【版权提示】观研报告网倡导尊重与保护知识产权。未经许可,任何人不得复制、转载、或以其他方式使用本网站的内容。如发现本站文章存在版权问题,烦请提供版权疑问、身份证明、版权证明、联系方式等发邮件至kf@chinabaogao.com,我们将及时沟通与处理。