导读:冷镦成形装备行业技术主要特点。冷镦成形装备属于机床行业中的金属成形机床,它主要以盘料或棒料为原料,利用冷镦成形技术,连续生产螺栓﹑螺母﹑销钉﹑钢球、滚柱等紧固件及形状复杂的伞齿轮轴﹑球头销﹑火花塞、刹车轴、转动轴、套筒扳手、轮毂螺丝、万向轴承、五金件等异形件等。
参考《2016-2022年中国冷镦钢行业发展态势及十三五运行态势预测报告》
1、产品概况
冷镦成形装备属于机床行业中的金属成形机床,它主要以盘料或棒料为原料,利用冷镦成形技术,连续生产螺栓﹑螺母﹑销钉﹑钢球、滚柱等紧固件及形状复杂的伞齿轮轴﹑球头销﹑火花塞、刹车轴、转动轴、套筒扳手、轮毂螺丝、万向轴承、五金件等异形件等。冷镦成形装备通常由床身、主滑台、主曲轴传动、机械手、送料、动模机构、定模机构、顶料机构、切料机构、电气控制、润滑冷却系统、外罩等主要功能部件构成,是一种高精、高效、优质、低耗、实现少无切削工艺的锻压成形机械,可实现连续、多工位、自动化、大批量成形生产的功能。
冷镦成形技术是利用金属材料塑性变形原理,在常温条件下,将金属线材装入模具型腔内,在外力作用下迫使金属线材产生塑性流动,并通过动模和定模的间隙和出口,使得金属线材实现镦粗、缩径、切边或挤出(半)空心等效果,从而获得所需几何形状及尺寸并具有较高力学性能挤压件的工艺技术。冷镦成形技术的主要特点如下:
(1)材料利用率较高
冷镦成形是利用金属的塑性变形来制成所需形状的金属零件,与切削、铸造等加工方法相比,可大幅度降低金属材料消耗,提高金属材料利用率,其中杆类产品材料利用率可达 99%,筒类产品由于需要打通孔,即需要冲掉一部分金属材料,材料利用率也能达 90%以上,从而减少了金属材料浪费。
(2)材料力学性能较高
冷镦成形是在常温条件下金属材料纤维随模具形成一定形状的流线并呈连续状,与切削加工相比,冷镦成形的金属材料晶粒无断开,其抗拉强度比切削加工有较大程度提高。
(3)表面粗糙度和尺寸精度较好
冷镦加工的金属零件表面粗糙度为 Ra0.4-Ra12.5μm,精度达 IT7-IT10 级,制得的金属零件表面粗糙度﹑尺寸精度相对较好。
(4)生产效率高,适合大批量生产
使用冷镦成形工艺代替切削加工制造紧固件、异形件,可使生产效率得到大幅提升,尤其是采用多工位冷镦成形装备可实现各道工序在一台设备上同时加工,较大程度提高了加工效率,也节约了生产成本,适合大批量生产。
(5)可加工形状复杂的、难以切削的金属零件
采用冷镦成形工艺可以加工出形状复杂、难以切削的金属零件,如异形截面、复杂内腔、内齿及表面看不见的内槽等,另外部分金属材料由于难以切削只能采用冷镦成形工艺。
随着现代工业的迅速发展及机械零件复杂程度的不断提高,传统生产制造技术难以适应高强度、非标复杂异形件尤其是特殊零件的生产制造,冷镦成形装备因其加工效率高、成形质量好的显著优势适应了异形件及特殊零件的生产制造需求,可用于汽车、航空航天等行业的非标复杂异形件及特殊零件的制造。当前,冷镦成形装备已成为主要的紧固件、非标异形件成形制造机械,广泛应用于汽车、铁路、航空航天、电力、机械、电器、电子、军工、船舶、石油化工、建筑等行业和领域的紧固件、非标异形件的制造。
冷镦成形装备的类型主要包括:单、双击冷镦机,多工位冷镦机等。其中,多工位冷镦机是将多个成形工序结合在一起,实现各道工序在一台设备上同时加工,极大减轻劳动强度、减少操作人员及占用生产场地的高端成形装备。因此,当形状比较复杂,需要在两个以上凹模中成形时,采用多工位冷镦机进行生产较为合适。此外,随着塑性加工技术的进步,加工的产品种类日益增多:材料方面,朝着合金钢、不锈钢等高强度钢、难加工材料方向发展;形状方面,朝着复杂形状方向发展;尺寸方面,朝着大尺寸方向发展。多工位冷镦机具备生产效率高、成形效果好、制造精度高等特点,符合上述发展方向,代表了目前冷成形制造装备的最高技术水平。
以生产下图中的自行车零件为例,若采用冷镦机制造,材料利用率将超过90%,远高于传统制造方法,且生产速度、制造精度以及最终产品的力学性能均优于传统制造方法。图示如下:
资料来源:公开资料,观研网整理,转载请注明出处(ww)。
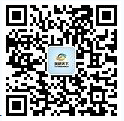
【版权提示】观研报告网倡导尊重与保护知识产权。未经许可,任何人不得复制、转载、或以其他方式使用本网站的内容。如发现本站文章存在版权问题,烦请提供版权疑问、身份证明、版权证明、联系方式等发邮件至kf@chinabaogao.com,我们将及时沟通与处理。