从产业链各环节来看,上游环节利润最高,本体企业利润微薄。上游核心零部件的性能直接决定了机器人的整体性能,具有技术含量高、易形成垄断的特点,也是整个产业链中利润最高的环节。而本体环节,通过采购零部件,自行设计制造非核心部件(基座、机身、机械臂、传动部件等)完成本体组装。外资品牌并不会把本体作为利润的中心,而是一个承上启下的环节。另一方面,单一本体厂商在市场推广方面会较为依赖系统集成商的支持,发展空间受到牵制。
我们以纳博和哈默纳科做零部件企业代表,以喷涂领域的杜尔集团作为系统集成商的代表。根据Bloomberg数据,纳博和哈默纳科的平均营业利润率分别为24%和10%,而杜尔集团的平均营业利润率为7%。零部件业务才是整个机器人产业链最核心的利润中心。
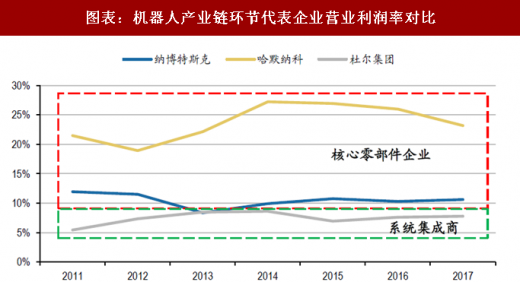
从全球范围来看,较为成功的大厂商一般都采用零部件+本体+集成的全产业链模式。以德国库卡为例,库卡以下游的汽车领域系统集成为切入口,最终实施产业链一体化模式。
汽车工业的特点就是快节奏的流水线式生产,这种制造方式有利于将每个环节分解成很基本的标准化工序,而库卡受益于德国巴伐利亚的产业集群,通过运用美国Unimation五轴机器人汽车产业提供焊接与汽车侧板加工系统,随后自主研发了全球第一台六轴机器人Famulus。1996年,KUKA拆分为机器人公司与焊接设备公司,机器人业务成为独立企业,并成长为国际四大家族之一。
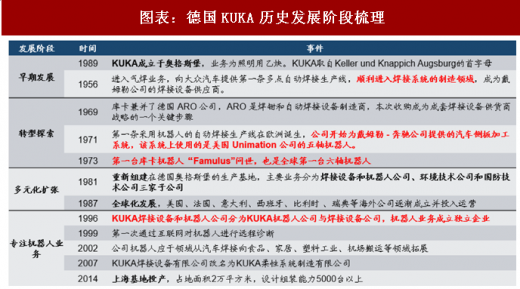
我们对比了不同商业模式的盈利能力。全产业链的代表生产企业包括国际机器人四大家族,系统集成的代表性企业为杜尔集团和拓斯达。从毛利率水平来看,发那科盈利能力领先,这主要来源于两个方面:1.伺服系统、控制系统与机床产生协同效应;2.软件业务毛利较高。而库卡整体毛利率被系统板块拖了后腿,机器人业务的毛利率可达到35%左右。单一的系统集成商杜尔集团毛利率水平较之四大家族最低,徘徊在20%左右。因此,从毛利率角度看,单一系统集成商的盈利能力并不如全产业链形式的四大家族。
参考观研天下发布《2018年中国服务机器人市场分析报告-行业运营态势与发展趋势预测》
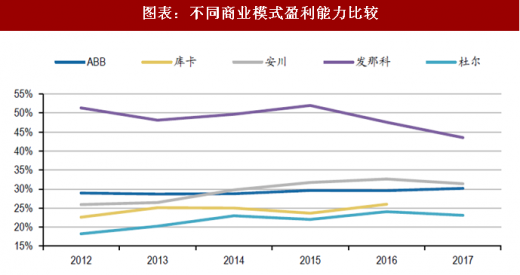
德国库卡从最初的汽车焊接,到本体制造,再到后期的控制器、伺服电机自制,已经走出了一条从下游系统集成向上游核心零部件的发展道路。从国内代表性企业对机器人产业链技术的掌握情况来看,埃夫特主要采用“本体+系统集成”模式,近年也开始进行核心零部件的研发,逐步向全产业链模式转型。
拓斯达和埃斯顿能够真正实现零部件的自主化。其中,拓斯达由下游系统集成向本体、零部件延伸,已经掌握了控制器和配合控制器的伺服驱动两类核心零部件;而埃斯顿则依托原有主业,向下游拓展,目前已能实现控制器和伺服系统完全自主生产,以及多关节机器人中的手腕关节(5-6轴)的减速器生产(根据年报的披露,公司自主研发了双曲面齿轮减速装置,其他关节高精度的精密减速器主要采购自日本的纳博特斯克)。
核心零部件的加速突破,有利于国内企业向一体化模式探索。我们认为,全产业链模式是当下工业机器人企业的发展趋势,集团将任务拆解、分工,各个环节转化为企业内部生产,使生产过程更加稳定,从而保障较高的盈利能力。
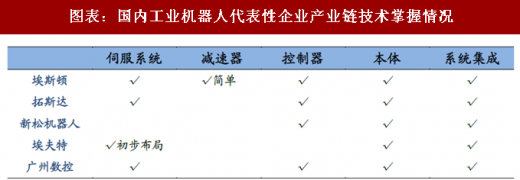
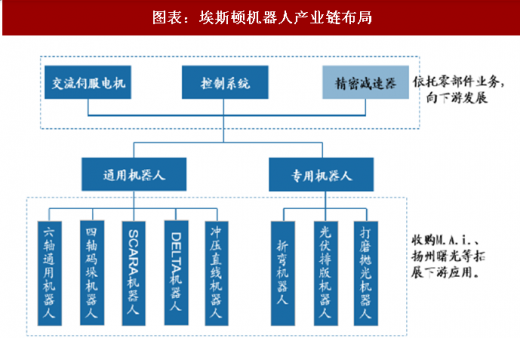

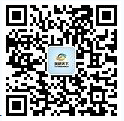
【版权提示】观研报告网倡导尊重与保护知识产权。未经许可,任何人不得复制、转载、或以其他方式使用本网站的内容。如发现本站文章存在版权问题,烦请提供版权疑问、身份证明、版权证明、联系方式等发邮件至kf@chinabaogao.com,我们将及时沟通与处理。