芯片设计是将系统、逻辑与性能的设计要求转化为具体的物理版图的过程,也是一个把产品从抽象的过程一步步具体化的过程。这一环节输出的是集成电路设计图纸, 晶圆制造的过程是设计成果转化成最终物理产品的过程。通过一定的工艺方式在硅片衬底上制造出电路所需要的晶体管、二极管、电阻器和电容器等元件用,并连接起来,形成具有特定计算能力的芯片(Die,裸片)。
封装是指把晶圆制造环节所生产的裸片放在一块起到承载作用的基板上,并把管脚引出来,然后固定包装成一个整体。芯片面积与封装面积比值可以用来衡量封装技术的先进性。
测试包括芯片设计中的设计验证、晶圆制造中的晶圆检测(Probe Test)和封装完成后的成品测试(Final Test)。一般将封装后的测试环节与封装环节合称为封装测试。
根据 WSTS 统计,2015 年全球芯片设计、晶圆制造和封装测试的收入分别约占产业链整体销售收入的 27%、51%和 22%。
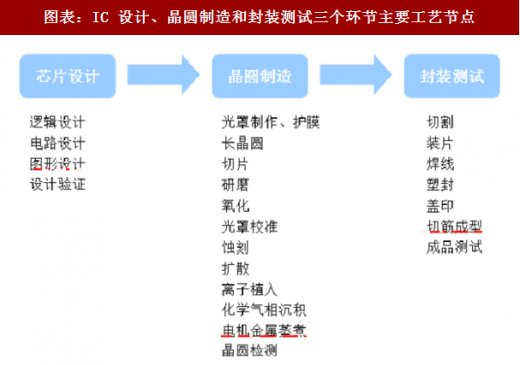
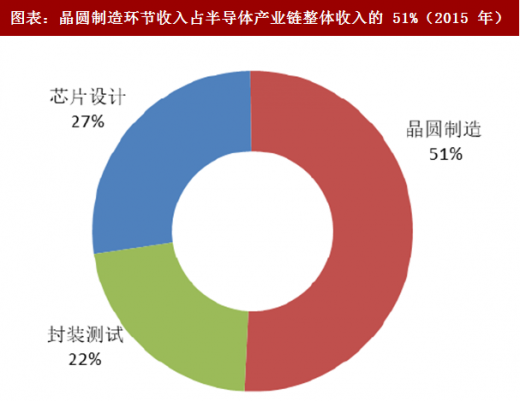
二、半导体行业发展过程是一个逐步专业化分工的过程
早期的集成电路企业以 IDM(Integrated Device Manufacturing)模式为主,也称为垂直集成模式,即 IC 制造商自行设计、并将自行生产加工、封装、测试后的成品芯片销售。目前这类企业典型包括三星(Samsung)、英特尔(Intel)等。半导体设备行业率先于 1960 年代分离出来,成为独立的公司。此后 EDA(电子设计自动化)软件企业也于 1970 年代分离出来。
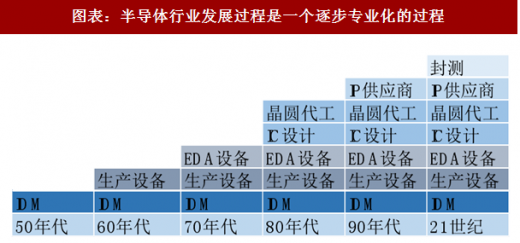
参考观研天下发布《2018年中国半导体市场分析报告-行业深度调研与投资前景预测》
与半导体工艺技术的进步同步出现的是成本的飙升。
1995 年以来,芯片制造工艺经历了从 0.5 微米到目前 28nm、 16/14nm 的发展过程,从 65nm 开始,晶圆制造生产线投资呈几何级数的增长。以芯片制造过程中必须使用的光罩(MASK)为例,55nm 的 MASK 费用约为 400 万人民币,40nm 的 MASK 费用约为 700 万人民币,28nm 的 MASK 费用约为 1,500 万人民币左右,16nm 的 MASK 费用更高达 4,000 万人民币左右。晶圆厂的投资更是水涨船高,以月产 3 万片 12 寸 20nm 制程的晶圆生产线为例,建造成本约为 70 亿美元。台积电披露其最新 7nm 工厂预计投资将达到 5000 亿新台币(约合 170 亿美金)。随着集成电路制程节点的缩小,制造技术难度成倍增加,能跟随工艺发展的制造厂商越来越少。
三、投资规模增加催生 Fabless 模式应运而生
1987 年台积电(TSMC)成立,开创新提出了 Foundry 模式,专注代工生产,为客户提供芯片生产和测试服务。与台积电 Foundry 模式对应,其客户可以专注于芯片设计开发,而不需要自建工厂生产,被称为 Fabless(无工厂)模式。典型的 Fabless 公司包括 ARM、AMD 和高通等。国内绝大多数芯片企业都采用 Fabless 模式,从而避免投入巨量资金建设工厂。
由于 Fabless 模式充分体现了专业化分工的优势,因此被大部分集成电路设计企业采用。这一模式下芯片设计企业( Fabless )、晶圆制造代工企业( Foundry )、封装测试企业
(Package&TestingHouse)分离成集成电路产业链中的独立一环,因此也被称为垂直分工模式。
目前虽然全球半导体前 20 大厂商中大部分仍为 IDM 厂商,如三星(Samsung)、英特尔(Intel)等,但由于近年来半导体技术研发成本以及晶圆生产线投资成本呈指数级上扬,更多的 IDM 厂商开始采用轻晶圆制造(Fab-lite)模式,即将晶圆委托晶圆制造代工企业厂商制造,甚至直接变成独立的芯片设计企业,如超微(AMD)、恩智浦(NXP )和瑞萨(Renesas)等,垂直分工已成为半导体行业经营模式的发展方向。
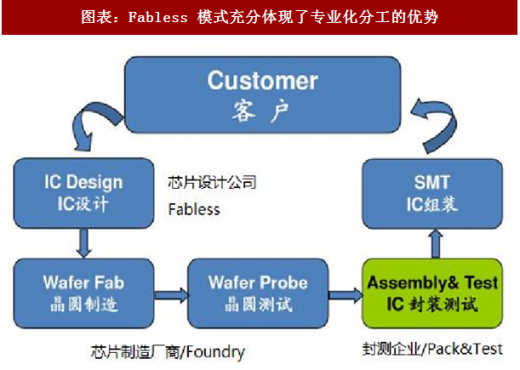
在垂直分工模式下,IC 设计企业( Fabless )只需要完成芯片开发与销售工作即可,晶圆制造代工企业( Foundry )与封装测试企业(Package & Testing House)通过外包的形式完成制造工作。Fabless 模式大大降低了 IC 行业的进入门槛,目前国内 IC 设计公司大多数都采用了 Fabless 模式,典型有海思半导体(HiSilicon)、展讯(SpreadTrum)等。同时一批专业代工企业也逐步发展起来,如晶圆代工企业中芯国际(SMIC)、长电科技等。
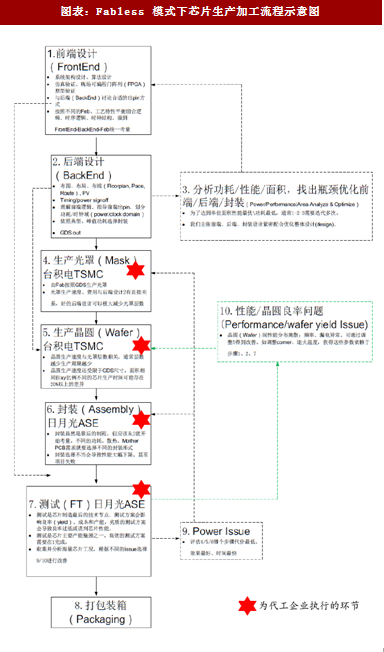
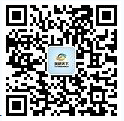
【版权提示】观研报告网倡导尊重与保护知识产权。未经许可,任何人不得复制、转载、或以其他方式使用本网站的内容。如发现本站文章存在版权问题,烦请提供版权疑问、身份证明、版权证明、联系方式等发邮件至kf@chinabaogao.com,我们将及时沟通与处理。